Dual Orin Controller: The Ideal Safety-Critical Platform for Autonomous Vehicles
As technology evolves, the automotive industry is constantly seeking ways to make driving safe, reliable, and autonomous. In this blog post, we’ll explore the features, functionality, and the impact that a platform based on dual Nvidia’s AGX Orin modules offers for the future of vehicle safety during operation. Additionally, we will elaborate on the concept of safety-critical systems and highlight the distinctions between safety-critical functionalities and ADAS (Advanced Driver Assistance System).
The Jetson AGX Orin is designed for advanced robotics and AI edge applications for manufacturing, logistics, retail, service, agriculture, smart city, healthcare, and life science. Dual Orin (2 Orin devices on the same motherboard) offers system redundancy, which refers to the presence of backup or duplicate components that can take over in the event of a failure in the primary system.
ADAS provides driver assistance and convenience, but it is not solely responsible for critical functions that impact safety. Safety-critical functions encompass components directly involved in critical functions such as braking and collision avoidance. Safety-critical systems follow strict standards to ensure reliable operation.
What is Orin?
The NVIDIA Jetson Orin solution is a SOM (system-on-module) with CPU, GPU, memory, power management, and various high-speed interfaces embedded on a single board. NVIDIA Jetson brings accelerated AI performance to the edge in a power-efficient and compact form factor. The Jetson family of modules all use the same NVIDIA CUDA-X™ software, and support cloud-native technologies like containerization and orchestration to build, deploy, and manage AI at the edge.
NVIDIA’s Orin platform (SoC) has three series for its Jetson products:
- Jetson AGX Orin series
- Jetson Orin NX series
- Jetson Orin Nano series
NVIDIA Jetson Orin modules provide 275 TOPS of AI performance and which increases the performance 8 times compared to Jetson Xavier for multiple concurrent AI inference pipelines, in addition to high-speed interface support for multiple sensors.
One of the major features of NVIDIA Jetson Orin is the DLA (Deep Learning Accelerator) which supports next-generation NVDLA 2.0 with 9x the performance of NVDLA 1.0. It enables the GPU to run more complex networks and dynamic tasks.
A Comparison of Orin with Traditional CPU/GPU
Now, let’s delve into a comparison between traditional processors and Orin by examining the following key features:
- Architecture
NVIDIA Jetson Orin is designed specifically for autonomous machines and edge computing. Jetson AGX Orin modules feature the NVIDIA Orin SoC with a NVIDIA Ampere architecture GPU, Arm® Cortex®-A78AE CPU, next-generation deep learning and vision accelerators, and a video encoder and a video decoder making it highly optimized for tasks like computer vision, deep learning, and robotics.
Traditional CPUs (Central Processing Units) and GPUs (Graphics Processing Units) are more general-purpose processors designed for a wide range of computing tasks, including running operating systems, executing applications, and performing graphics rendering.
- Power Efficiency
NVIDIA Jetson AGX Orin series modules are designed with a high efficiency Power Management Integrated Circuit (PMIC), voltage regulators, and a power tree to optimize power efficiency. It strikes a balance between performance and energy consumption, allowing for longer battery life and reduced power requirements in embedded systems.
While traditional CPUs and GPUs can offer high computational power, they are generally more power-hungry compared to specialized SoCs like Jetson Orin. They are commonly found in desktops, servers, and workstations where power consumption is less constrained.
- AI Performance
The NVIDIA Jetson AGX Orin series provides server class performance, delivering up to 275 TOPS of AI performance for powering and managing autonomous systems. Its high performance is ideal for tasks like object detection, image recognition, natural language processing, and autonomous navigation.
Traditional CPUs and GPUs can also handle AI workloads, but they do not provide the same level of performance or efficiency as AI-focused modules like Jetson Orin. GPUs, in particular, have been utilized for parallel processing in deep learning tasks, but they are less power-efficient compared to specialized AI chips.
In addition, the Jetson Orin modules are extremely compact enabling the compute platform to have reduced size and weight – critical for autonomous robots and UAVs.
- Software Ecosystem
NVIDIA Jetson Orin is part of NVIDIA’s Jetson platform, which offers a comprehensive software stack, including drivers, libraries, and frameworks specifically optimized for AI and autonomous applications. It supports popular AI frameworks like TensorFlow, PyTorch, and CUDA, providing developers with familiar tools and resources.
Traditional CPUs and GPUs also have a mature and extensive software ecosystem with support for a wide range of operating systems, development tools, and programming languages. They are compatible with various software frameworks, including those used for AI, but may require additional configuration and optimization for specific AI workloads.
Key differences between NVIDIA Orin and Xavier
NVIDIA Jetson AGX Xavier and NVIDIA Jetson AGX Orin have the same physical footprint and are pin compatible while also being in the same price range with one major difference that the Orin offers much higher performance.
The biggest change change is moving from Nvidia’s Carmel CPU clusters to the ARM Cortex-A78AE on Jeston AGX Orin.
The Orin CPU complex is made up of 12 2.2 GHz cores, each with 64KB Instruction L1 Cache and 64KB Data Cache, and 256 KB of L2 Cache. This enables x1.85 performance increased compared to the eight core Carmel CPU on Jetson AGX Xavier.
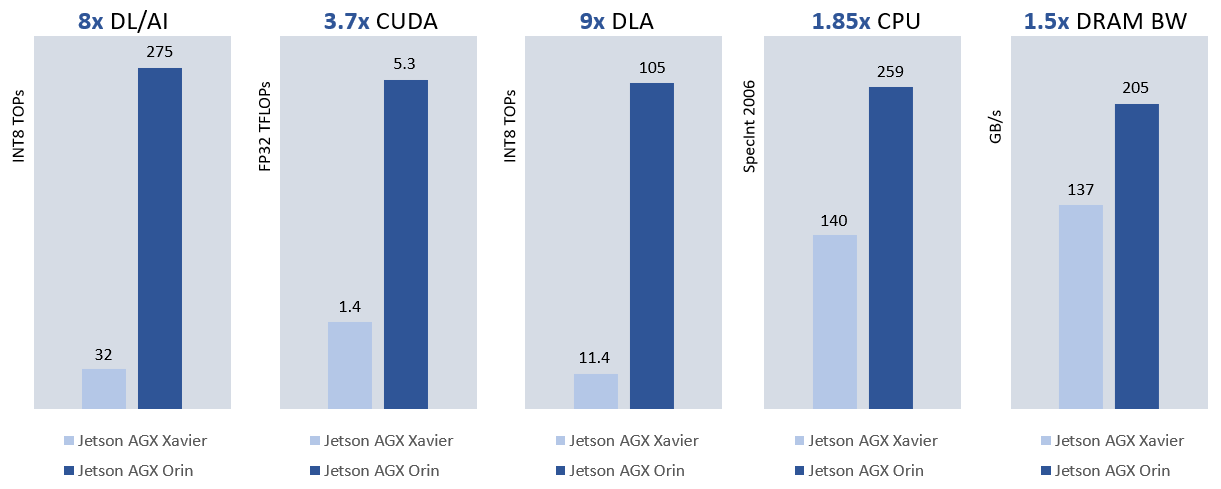
Jetson AGX Orin modules deliver an AI performance that can reach 275 TOPS with up to 64 GB of memory, compared to 32 TOPS with up to 32 GB of memory for Jetson Xavier.
Jetson AGX Orin 64GB has 2048 CUDA cores and 64 Tensor cores with up to 170 Sparse TOPS of INT8 Tensor compute, and up to 5.3 FP32 TFLOPs of CUDA compute, while Jetson Xavier has only up to 1.4 FP32 TFLOPs of CUDA compute. Ampere GPU brings support for sparsity, a fine-grained compute structure that doubles throughput and reduces memory usage.
DLA 2.0 provides a highly energy efficient architecture. With this new design, NVIDIA increased local buffering for even more efficiency and reduced DRAM bandwidth. DLA 2.0 additionally brings a set of new features including structured sparsity, depth wise convolution, and a hardware scheduler. This enables up to 105 INT8 Sparse TOPs total on Jetson AGX Orin DLAs compared with 11.4 INT8 Dense TOPS total on Jetson AGX Xavier DLAs.
The 12-core CPU on Jetson AGX Orin 64GB enables 1.85 times the performance compared to the 8-core NVIDIA Carmel CPU on Jetson AGX Xavier. Customers can use the enhanced capabilities of the Cortex-A78AE including the higher performance and enhanced cache to optimize their CPU implementations.
Jetson AGX Orin modules bring support for 1.5 times the memory bandwidth and 2 times the storage of Jetson AGX Xavier, enabling 32GB or 64GB of 256-bit LPDDR5 and 64 GB of eMMC. The DRAM supports a max clock speed of 3200 MHz, with 6400 Gbps per pin, enabling 204.8 GB/s of memory bandwidth.
The combination of NVIDIA’s processing capabilities and power efficiency, along with its safety-critical features, makes it the ideal solution for autonomous applications.
Safety Critical Software in Automotive Safety
Functional safety in processor-based systems is particularly critical in automotive applications. Apart from the ongoing shift towards autonomous vehicles, cars are increasingly dependent on microprocessors to carry out essential operations and must have redundant systems to enable safety in the event of a component failure.
ISO 26262 serves as the globally recognized standard for ensuring functional safety in the automotive industry. This international standard encompasses both the hardware and software components of a vehicle’s electrical and electronic (E/E) systems. Throughout the development process, ISO 26262 outlines specific requirements that must be fulfilled to ensure the safety-related functionality of the system, along with the corresponding processes, methodologies, and tools. By adhering to the ISO 26262 standard, manufacturers can ensure that sufficient safety measures are implemented and maintained throughout the entire lifespan of the vehicle.
ISO 26262 offers comprehensive guidelines on determining acceptable risk levels for systems or components and documenting the testing process. It encompasses the following key aspects:
- Defines an automotive safety lifecycle that covers management, development, production, operation, service, and decommissioning stages, allowing for customization of activities during each phase.
- Implements an automotive-specific risk-based approach for classifying risk levels known as Automotive Safety Integrity Levels (ASILs).
- Utilizes ASILs to specify the required safety measures for achieving an acceptable residual risk.
- Establishes requirements for validation and confirmation measures to ensure the attainment of a satisfactory level of safet.y
Dual AGX Orin Controller Overview
The Dual AGX Orin system offers superior computing power compared to a single Orin solution making it preferable for specific applications that require higher computational power and redundancy.
The Dual Orin Controller’s computational capacity enables it to handle multiple complex tasks simultaneously. This capability is particularly valuable in scenarios where there is a need for concurrent processing of multiple data streams from various sensors, making it suitable for advanced autonomous machines, commercial vehicles, unmanned distribution vehicles, and unmanned cleaning vehicles.
In safety-critical applications, redundancy is essential to ensure system reliability. The Dual Orin Controller’s utilization of two AGX Orin modules provides a level of redundancy and failover capabilities. If one module encounters an issue, the other can continue functioning, minimizing the risk of critical system failures and improving the overall reliability of the autonomous machine.
Tauro Technologies TT300 Dual AGX Orin Controller
Tauro Technologies’ TT300 Dual AGX Orin compute platform provides exceptional computing power, low energy consumption, in a compact form factor.
With up to 400/550 TOPS of AI performance this product can be used in autonomous vehicles, UAVs and robotics. The product is designed for high reliability and redundancy, provides multi-sensor clock synchronization with sub-nanosecond accuracy and millisecond latency for precise timing.
Let’s take a closer look at TT300 key features:
- Dual Orin Controllers 550 TOPS
The TT300 board is equipped with two powerful Orin controllers, delivering combined processing power of 550 TOPS. This immense computing power enables lightning-fast data processing and analysis, making it ideal for handling complex AI workloads.
- Infineon TC397 Safety MCU
Ensuring the highest levels of safety and reliability, the TT300 board incorporates the Infineon TC397 safety microcontroller to support safety requirements up to ASIL-D. This MCU plays a crucial role in safeguarding the system against potential hazards and maintaining the integrity of critical operations.
- 100Base-T1/1000Base-T1 Ethernet
To facilitate efficient and reliable data communication, the TT300 board is equipped with both 100Base-T1 and 1000Base-T1 Ethernet interfaces. These interfaces enable fast and secure data transfer, ensuring smooth integration into existing vehicle network infrastructures.
- Wi-Fi/4G/5G
TT300 board supports Wi-Fi, 4G LTE and 5G connectivity, enabling seamless wireless communication and remote access. Whether you need to stream data, receive updates, or control the board remotely, these connectivity features have you covered.
- GMSL2 Interface for Hi-Res Cameras
The TT300 board features a GMSL2 interface, enabling reliable connection with high-resolution cameras. This interface supports the transmission of data between the controller and cameras, ensuring high-quality image and video feed for AI applications such as ADAS, object detection, tracking, and recognition.
GMSL cameras are becoming a defacto standard in automotive industry where high data rates and long-distance support is required, addressing the need to transport higher video data rates in automotive video systems.
In addition to high bandwidth transmission, long-distance support, and low latency, GMSL cameras also come with the following features:
- Virtual channel support
- GMSL1 and GMSL2 backward compatibility
- Video duplication
- Automatic Repeat Request (ARQ) feature
- Compatibility with ARM platforms like the NVIDIA Jetson series
I/O Capabilities
TT300 is powered by two NVIDIA Jetson AGX Orin modules and Infineon TC397 safety MCU enables the design to meet ASIL-D highest reliability requirements. The I/O capabilities of the product include automotive as well as industrial ethernet interfaces, USB, wireless connectivity over 4G/5G and Wi-Fi, GMSL camera and LVDS radar interfaces for ADAS applications, as well as CAN and LIN interfaces for automotive and robotics applications routed to CMC connector. Wide selection of interfaces and customization options makes this device easily adaptable to various use cases and application scenarios.


Conclusion
Tauro Technologies’ TT300 is one of the industry’s first platforms to offer the Nvidia Jetson Orin AGX in a redundant safety critical setting. This is an ideal system for self-driving vehicles in automotive, mining, and defense sectors as well as autonomous robots and UAVs that require exceptional performance and functional safety certification.
We can customize the I/O as well as the product packaging to fit your application requirements – contact us for details.